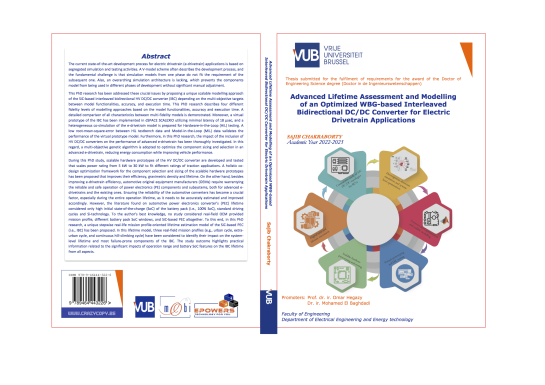
The current state-of-the-art development process for electric drivetrain (e-drivetrain) applications is based on segregated simulation and testing activities. A V-model scheme often describes the development process, and the fundamental challenge is that simulation models from one phase do not fit the requirement of the subsequent one. Also, an overaching simulation architecture is lacking, which prevents the components model from being used in different phases of development without significant manual adjustment.
This PhD research has been addressed these crucial issues by proposing a unique scalable modelling approach of the SIC-based interleaved bidrectional HV DC/DC converter (IBC) depending on the multi-objective targets between model functionalities, accuracy and execution time. This PhD researcg describes four different fidelity levels of modelling approaches based on the model functionalities, accuracy and execution time. A detailed comparison of all characteristics between multi-fidelity models is demonstrated. Moreover, a virtual prototype of the IBC has been implemented in dSPACE SCALEXIO utilizing minimal latency of 18 usec, and a heterogeneous co-simulation of the e-drivetrain model is prepared for Hardware-in-the-Loop (HiL) testing. A low root-mean-square-error between HiL testbench data and Model-in-the-Loop (MiL) data validates the performance of the virtual prototype model. Furthermore, in this PhD research, the impact of the inclusion of HV DC/DC converters on the performance of advanced e-drivetrain has been thoroughly investigated. In this regard, a multi-objective genetic algorithm is adopted to optimize the component sizing and selection in an advanced e-drivetrain, reducing energy consumption while improving vehicle performance.
During this PhD study, scalable hardware prototypes of the HV DC/DC converter are developed and tested that scales power rating from 5 kW to 30 kW to fit different ratings of traction applications. A holistics co-design optimization framework for the component selection and sizing of the scalable hardware prototypes has been proposed that improves their efficiency, gravimetric density and lifetime. On the other hand, besides improving e-drivetrain efficiency, automotive original equipment manufacturers (OEMs) require warrantying the reliable and safe operation of power electronics (PE) components and subsystems, both for advanced e-drivetrains and the existing ones. Ensuring the reliability of the automotive converters has become a crucial factor, especially during the entire operation lifetime, as it needs to be accurately estimated and improved accordingly. However, the literature found on automotive power electronics converter's (PEC) lifetime considered only high initial state-of-the-charge (SoC) of the battery pack (i.e., 100% SoC), standard driving cycles and Si-technology. To the author's best knowledge, no study considered real-field OEM provided mission profile, different battery pack SoC windows, and SiC-based Pec altogether. To this end, in this PhD research, a unique stepwise real-life mission profile-oriented lifetime estimation model of the SiC-based PEC (i.e., IBC) has been proposed. In this lifetime model, three real-field mission profile (e.g., urban cycle, extra-urban cycle, and continous hill-climbing cycle) have been considered to identify their impact on the system-level lifetime and most failure-prone components of the IBC. The study outcome highlights practical information related to the significant impacts of operation range and battery SoC features on the IBC lifetime from all aspects.