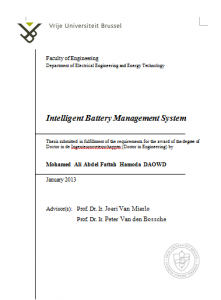
Global environment protection and energy preservation are the main reasons of the growing interest in electric vehicles (EV) due to their particular benefits for a healthier environment. Technological innovation to accelerate the deployment of clean vehicles has to be encouraged to overtake the barriers to EV development. Lithium based batteries are considered a most advanced battery technology, which can be designed for high energy or high power systems. However, individual battery cells never behave identical, due to the fabrication process and environmental conditions. In order to have a high-performance battery system, the battery cells should be continuously balanced to maintain the variation of the state of charge between the battery cells in a small range. Without an appropriate balancing system, the cell voltages will change over the operating time, while battery system capacity will decrease. These issues can limit the range of the electric vehicle and can shorten the lifetime of the battery cells. Battery management systems (BMS) play a vital role to improve the performance of the electric vehicle. BMS can protect the battery system from damage, can predict and extend the battery lifetime. Further, the BMS can maintain the battery system in good operating conditions. The BMS performs several tasks such as measuring the system voltage, current and temperature, the cellsā state of charge (SoC), state of health (SoH), and remaining useful life (RUL) determination, protecting the cells, thermal management, controlling the charge/discharge procedure, data acquisition, communication with on-board and off-board modules, monitoring, storing historical data and, most importantly, cell balancing. A lot of cell balancing/equalization methods have been considered in the literature. These balancing topologies can be categorized as either passive or active balancing systems. Most of the commercially available balancing systems are of the passive type. These systems can be acceptable for low power applications, however with high power applications the system losses will increase dramatically. Novel active balancing systems aim to reduce the system losses and size at an acceptable cost. In this dissertation an intelligent battery management system has been proposed to improve the performance of the battery system. The proposed BMS performs the key task of cell balancing as well as battery system charging/discharging control, thermal management and user input/output interfacing. In the framework of this thesis, various novel methodologies have been proposed. The procedures of the dissertation can be summarized in the following steps: Analysis of various battery models based on several standard tests and battery model simulation. Developing a novel battery model parameters estimation methodology based on MATLAB/SimulinkĀ® parameters estimation tool. Developing new electrical battery model, which can predict the battery behavior more accurately than the existing the battery models, encompassing a new methodology for the model parameters implementation. Presenting a state-of-the-art of the battery balancing management topologies including full detailed comparison of the employed balancing topologies. Developing a novel battery balancing system based on battery pack modularization, featuring different equalization systems that operate inside and outside the modules. From the point of view of the control strategy, the proposed balancing methodology is based on: Innovative single switched capacitor (SSC) control strategy to balance between the cells inside the modules. Novel utilization of isolated bidirectional dc-dc converter (IBC) to balance between the modules with the aid of the EV auxiliary battery. Implementing an experimental step-up for validation of the new proposed balancing system. The prototype battery pack of 12 Li-Ion series cells is divided into three modules with four cells each. Each cell has 20 Ah and 3.65 V, total pack nominal voltage is 43.8 V and capacity 0.876 KWh. Finally, the BMS proposed in the framework of this PhD can be considered as an attractive solution for high-performance clean vehicles.
Promotor: Prof. Dr. Joeri Van Mierlo