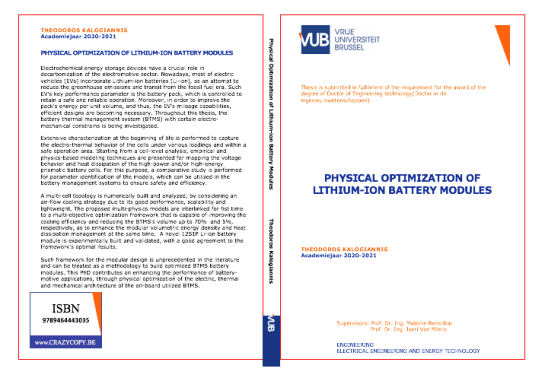
Electrochemical energy storage devices have a crucial role in decarbonization of the electromotive sector. Nowadays, most of electric vehicles (EVs) incorporate Lithium-ion batteries (Li-ion), as an attempt to reduce the greenhouse emissions and transit from the fossil fuel era. Such EV's key performance parameter is the battery pack, which is controlled to retain a safe and reliable operation. Moreover, in order to improve the pack's energy per unit volume, and thus, the EV's mileage capabilities, efficient designs are becoming necessary. Throughout this thesis, the battery thermal management system (BTMS) with certain electro-mechanical constrains is being investigated.
Extensive characterization at the beginning of life is performed to capture the electro-thermal behavior of the cells under various loadings and within a safe operation area. Starting from a cell-level analysis, empirical and physics-based modeling techniques are presented for mapping the voltage behavior and heat dissipation of the high-power and/or high-energy prismatic battery cells. For this purpose, a comparative study is performed for parameter identification of the models, which can be utilized in the battery management systems to ensure safety and efficiency.
A multi-cell topology is numerically built and analyzed, by considering an air-flow cooling strategy due to its good performance, scalability and lightweight. The proposed multi-physics models are interlinked for fist time to a multi-objective optimization framework that is capable of improving the cooling efficiency and reducing the BTMS's volume up to 70% and 5%, respectively, as to enhance the modular volumetric energy density and heat dissipation management at the same time. A novel 12S1P Li-ion battery module is experimentally built and validated, with a good agreement to the framework's optimal results.
Such framework for the modular design is unprecedented in the literature and can be treated as a methodology to build optimized BTMS battery modules. This PhD contributes on enhancing the performance of battery-motive applications, through physical optimization of the electric, thermal and mechanical architecture of the on-board utilized BTMS.